A-Maze-Ing Solvers
Overview:
Imagine a world where disabilities do not have an impact upon a person’s mobility and ability to navigate efficiently. When looking specifically at visual impairment, which would arguably be one of the most difficult disabilities to cope with, little to no technology exists to aid these people. At the current point in time, the main methods that people with visual impairments use for transportation are guide dogs and/or a red cane with a white tip. This method is practical at its core and completes its goal of safely guiding someone from point A to B, however this method does not take into account efficiency. In no way does this technology help visually impaired people to find the most efficient path to follow, rather it simply expects that they can rely on their other senses in order to find the best path.
Now imagine a hospital where patients are led from room to room in wheelchairs that drive themselves. The robot would be able to follow a common path, map out the area, and learn the shortest route from one place to another in the smallest amount of time. This technology could even be extended to transportation on a larger scale. If the wheelchair was designed for use on the street, it could be programmed to stop at places that are marked as caution areas, such as crosswalks or busy traffic areas that could be dangerous. Our robot could be connected through GPS and programmed to help people with various handicaps live easier lives. This could be modified in many other ways besides automated wheelchairs. Current technologies already exist using the concept we plan to explore. The Roomba, a robot vacuum, moves around the room vacuuming the things in its path. Other examples include parking sensors, mobile devices, and those sensors that stop the conveyor belt from moving at the cash register when your items get to the front.
 |
Proximity sensors in a conveyor belt |
 |
Proximity sensors in a car |
 |
Proximity sensors in a smartphone |
Anyone with blindness or a disability that requires a wheelchair would benefit from this type of machine. All of these influence direction and safety of the disabled person. There seems to be a lack of interest in solving this problem currently without the use of current technology. We are qualified to address this problem because we are motivated future mechanical engineers exploring the use of proximity sensors, motors and coding to create a project that if pursued further can be helpful to a lot of people.
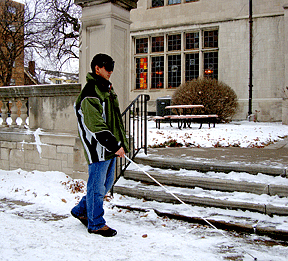 |
A man forced to navigate through the streets with a disability. |
 |
A hospital patient unable to navigate on their own two feet.
|
Description of Solution:
With the A-Maze-ing solver, we will be utilizing the capabilities of proximity sensors in a mobile robot in order to solve a maze in the most efficient manner. With these sensors, our robot will be able to detect the walls in front of it and send a signal, which tells the robot to turn and go about another direction, successfully navigating from point A to B. These applications can be stretched far beyond mazes and can potentially help with navigation for the visually impaired. In these situations, a robot could detect an obstacle and notify its owner to allow for more efficient travel methods and avoid collisions. We chose this problem because we feel that there should be easier and more efficient ways for people with disabilities to navigate their world.
Existing solutions to the aforementioned problem are fairly limited and have been used for too long. These could include walking sticks and seeing eye dogs. Our team believes that something much more than just these overused methods can be created. For example, imagine having a wheel chair that was also a machine with sensors on it that mapped out your world for you and could alert you of any oncoming obstacle or danger. The benefits pertaining to this idea would involve an easier life for certain groups in society. The expected price may vary, but we do not believe this to be a deterrence to the project. Our target audience would be either companies, such as hospitals, or people with disabilities, in which case health insurance should play a factor.
 |
MicroMouse example |
 |
Performing functions of human likeness |
MicroMouse Analysis:
Some materials needed to make the micromouse consist of 2 DC motors, a motor shield, one arduino kit, 3 wheels, a micromouse shell, proximity sensors, and one battery pack. The team will meet at least twice a week to go over coding, ideas, improvements, design, construction, testing, and prototyping. We will stay within our budget, provided by the competition guidelines, and utilize any other pieces that were found from recycled objects around the house. This will include taking apart old toys to find any other parts that will be useful.
The resources that are listed will be used to make the micromouse as agile, sleek, and functional as possible. Most of the previously mentioned items that are still needed will be bought at Adafruit, Pololu, Sparkfun and any other website we find that sells items for robotics.
 |
Important tools to our success |
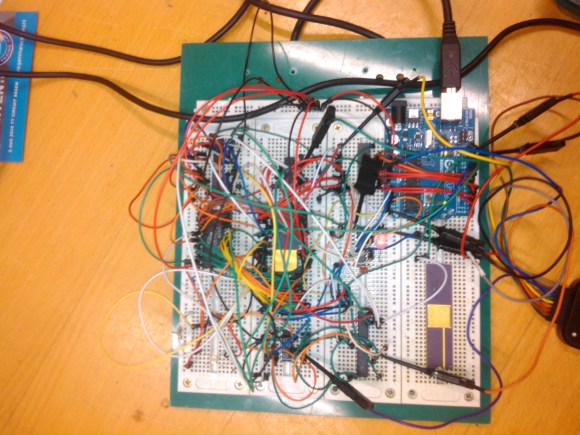 |
Intricate coding and wiring to transmit information to microprocessors |
Road Map:
Establishing a set amount of hours, based upon availability, will help make sure that we have sufficient time needed to work on the project and make sure it will be finished by the presentation date of December 4, 2014.
Steps:
The risks we will come across may consist of time constraints, Inconsistencies pertaining to the mouse following the correct path, a lack of availability of necessary pieces within our budget, and minor issues within the code. Risk is always a part of any experiment or project, but should not be a deterring factor. Take a risk and believe in the A-Maze-Ing Solvers!